Pressure Clamping System with High Rigidity and Precision PowRgrip
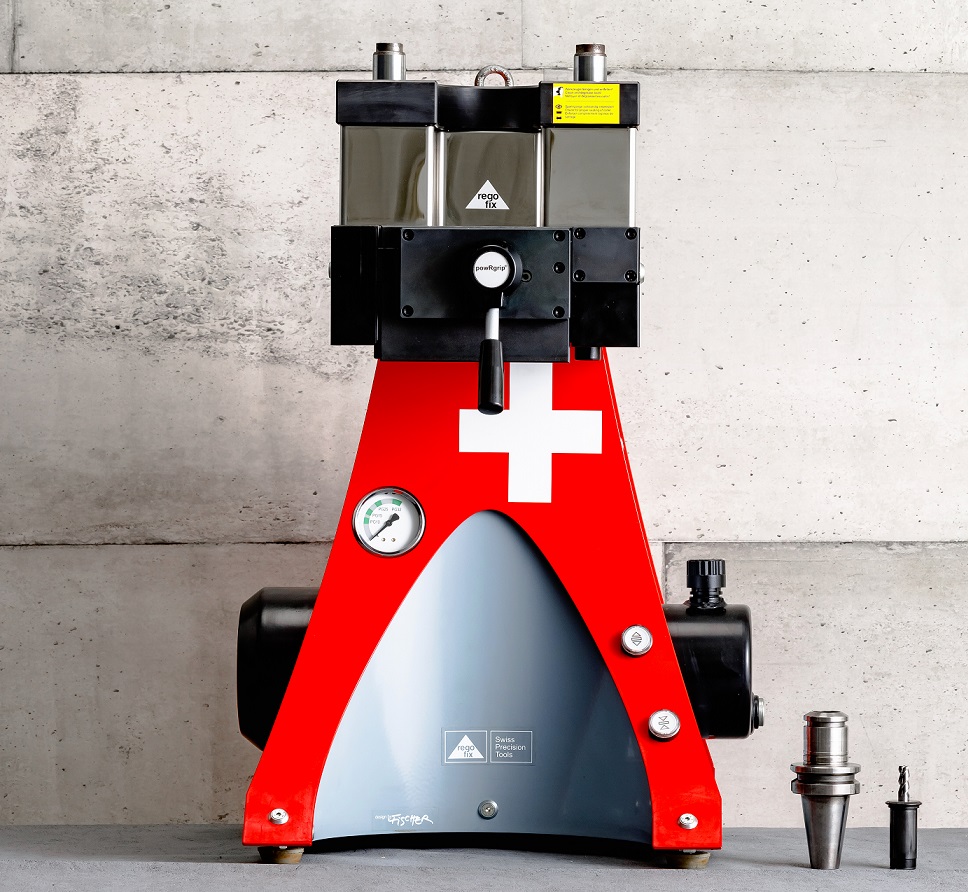
Pressure clamping system
This is high rigidity and precision tool clamping system.
REGO powRgrip allows to improve hole accuracy and surface roughness, and higher cutting speed.
This new pressure clamping system improves rigidity and accuracy compared to holder which is currerntly used.
-
・ Hydro chuck
・ Collet chuckHigh precision but low clamping force. It is not recommended for endmill machining.
-
・ Milling chuck
High clamping force but lower accuracy.
It is not recommended for drilling and reamer machining. -
・ Shrink fit chuck
High clamping force and precision.
Since heating is necessary for clamping and unclamping, it takes time to heat and cool, which could be a safety issue.
It cannot clamp HSS. It is necessary to prepare wide numbers of holders since it cannot use collet.
REGO powRgrip can solve all the problems!!
Clamping force is 2~3 times compared to hydro chuck and collet chuck.
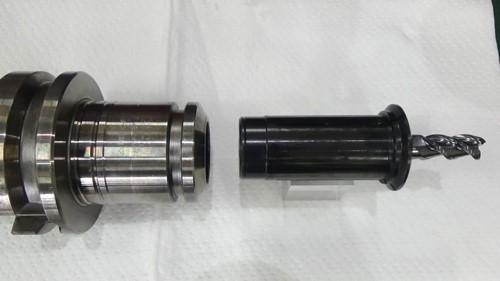
REGO powRgrip clamps whole shank.
By press fitting a 1° tapered collet into the holder and clamping it, stable machining is possible even under high speed cutting conditions.
On the other hand, general milling chucks and shrink fit chucks have a system that clamps in a relatively small area because the clamping force is concentrated on the tip of the holder.
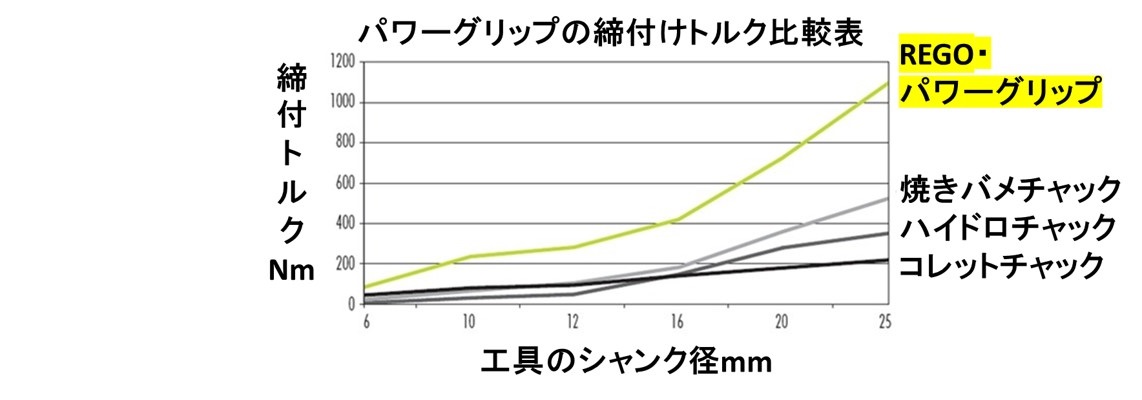
High runout precision
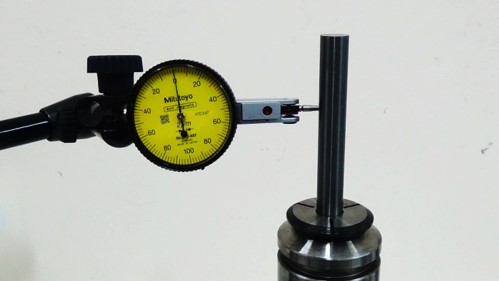
Total system runout TIR ≤ 3 μm at 3 x D *1*
Improves hole accuracy and surface roughness, and extends tool life.
*1 Clamps test bar (Runout accuracy of general milling chucks are 15~20 μm.)
Testing video
Specific features of REGO-FIX powRgrip
No indivisual clamping difference since it is press-fitted by a machine.
Maximum clamping force and low runout, even after 20,000 tool exchange.
Tool ready for use in less than 10 seconds without indivisual clamping difference. Very safe clamping and unclamping without use of heat and cooling.
Further possibilities only for pressure clamping system
It will allow to save manpower of tool clamping.
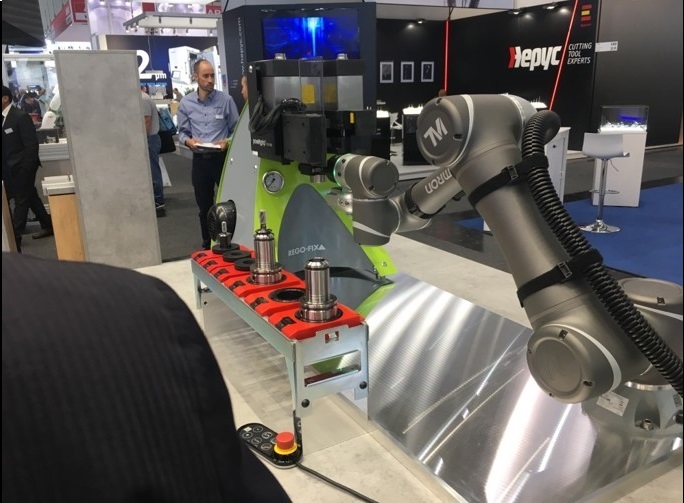
Product detail (PDF file)
-
Higher cutting speed
Machining cost will be saved by improving efficiency.
-
Improve machining accuracy
Stabilizing quality by improving surface roughness and hole accuracy.
-
Improve tool exchange process
Reducing tool exchange time and improving indivisual clamping difference