Chip evacuation performance comparison of taps
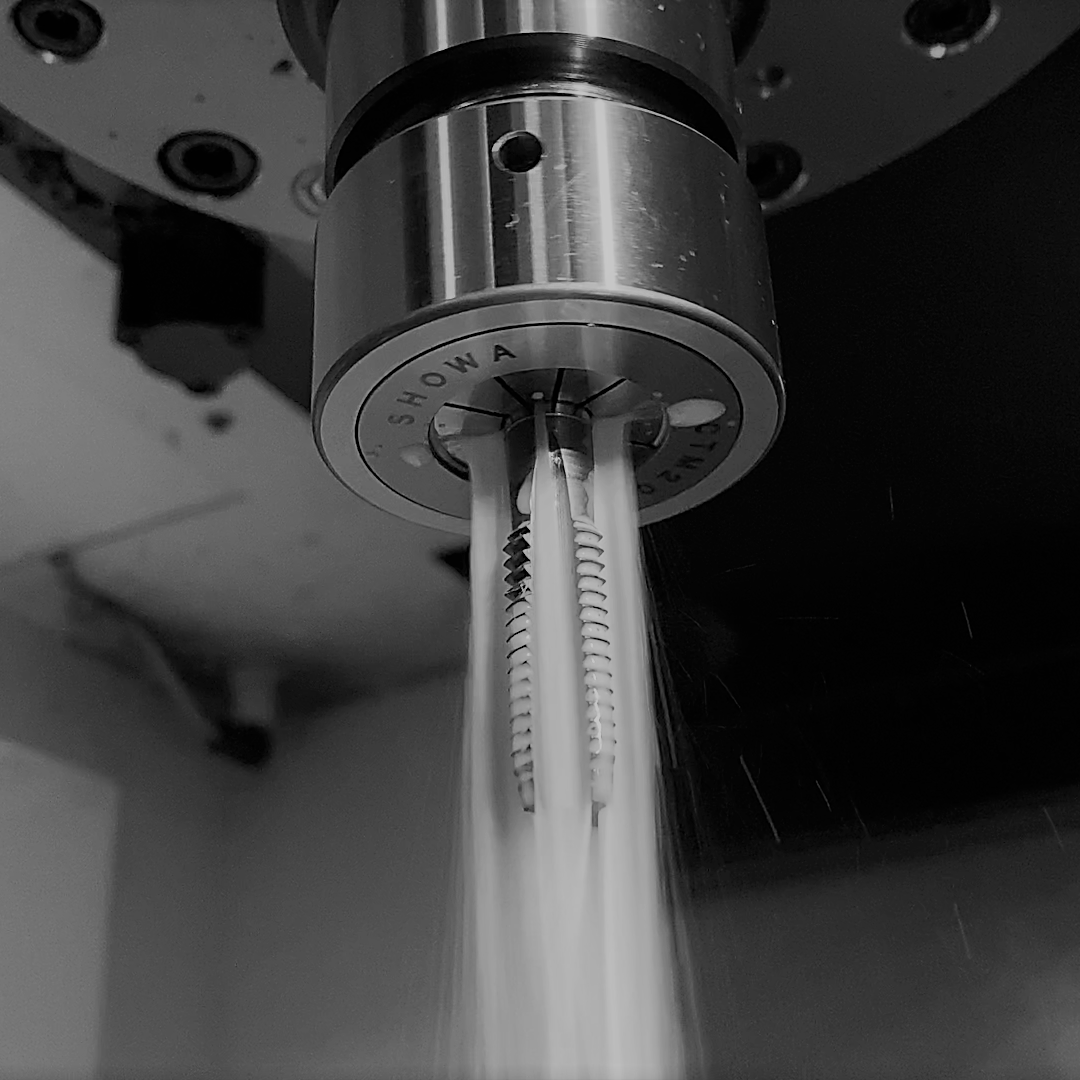
Center through vs. Collet through vs. Shank through
The tool life and cutting condition may be improved by optimal coolant supply.
INDEX
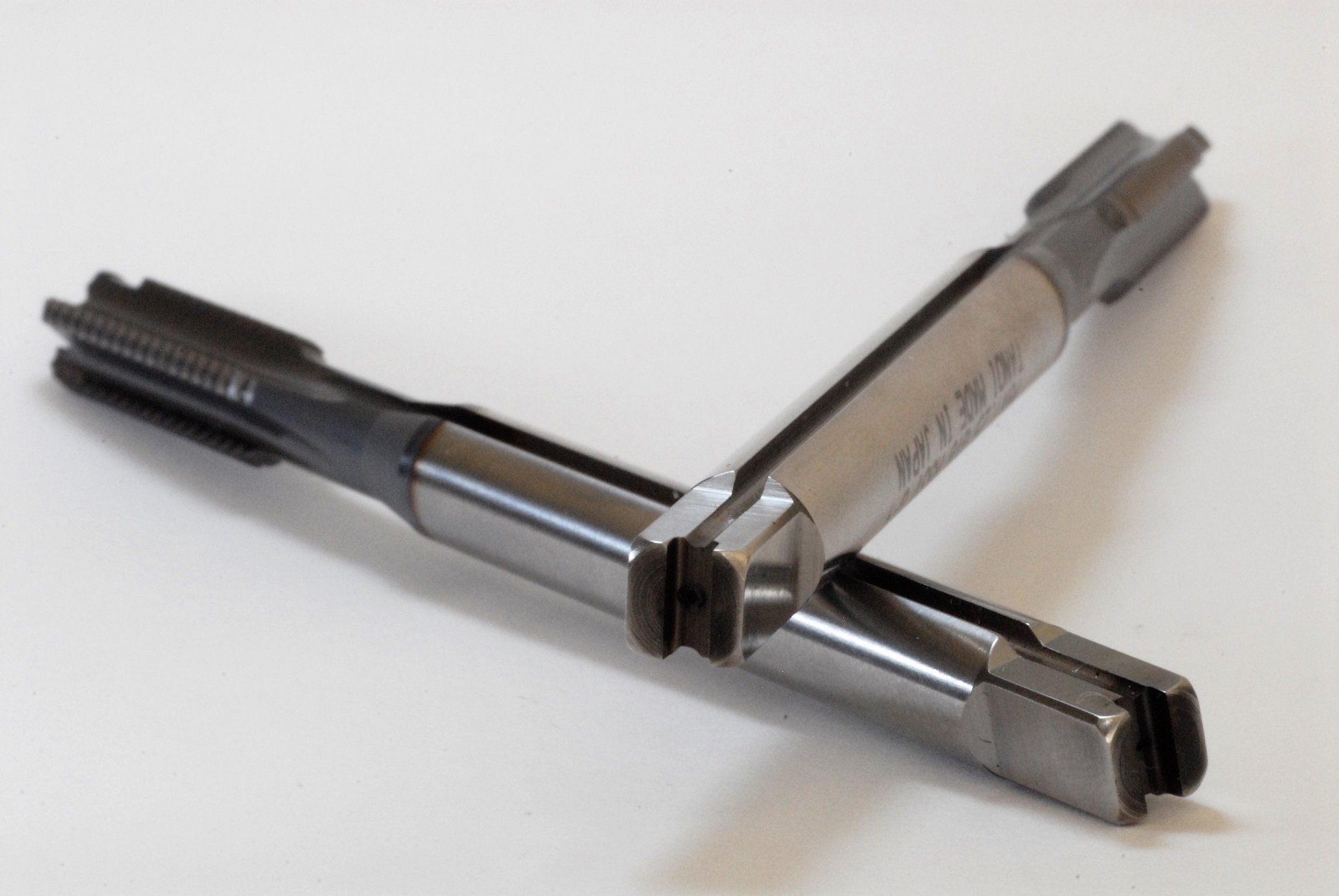
Outline
Speaking of taps, it is necessary to take measures against troubles caused by chips, but machining using taps has limited countermeasures than other machining.
This time, we will feature in Tanoi's zero chip tap, which is supplying coolant from the groove in the shank.
Forming taps, cutting taps, point taps, and carbide tools are standard inventory.
Available with castings, steels, and stainless steels, and aluminum.
Each features explanation
Center through
-
In case of blind hole:◎
Enough coolant discharge and excellent chip evacuation. -
In case of through hole:×
Coolant comes out from the hole, so it is difficult to supply coolant for machining points.
Collet through
-
In case of blind hole::×
It is not recommended because the coolant discharge and the chip evacuation will be from the same part, and the coolant will interrupt the chip evacuation. -
In case of blind hole:◎
Coolant is easily applied to the outer peripheral part of the tool, and chips are easily evacuated from the through hole side. However, if the projection are too long, the coolant will be diffused and the effect will tend to be lower.
Shank through
-
In case of through hole:〇
There are 2 grooves for coolant discharge. Since the coolant entry and chip evacuate groove are separated, it allows smooth discharge. Especially effective for aluminum and cast iron. -
In case of through hole:◎
The coolant is supplied from 4 grooves.
Test report
-
Machine
Mazak VCN-430A(BT40)
Coolant pressure:0.5MPa -
Workpiece clamping condition
Size: 100mm x 50mm x 30mm height x 2 blocks
Material: FC250
Compared with coated HSS for M12 course tap under Vc=10m/min.
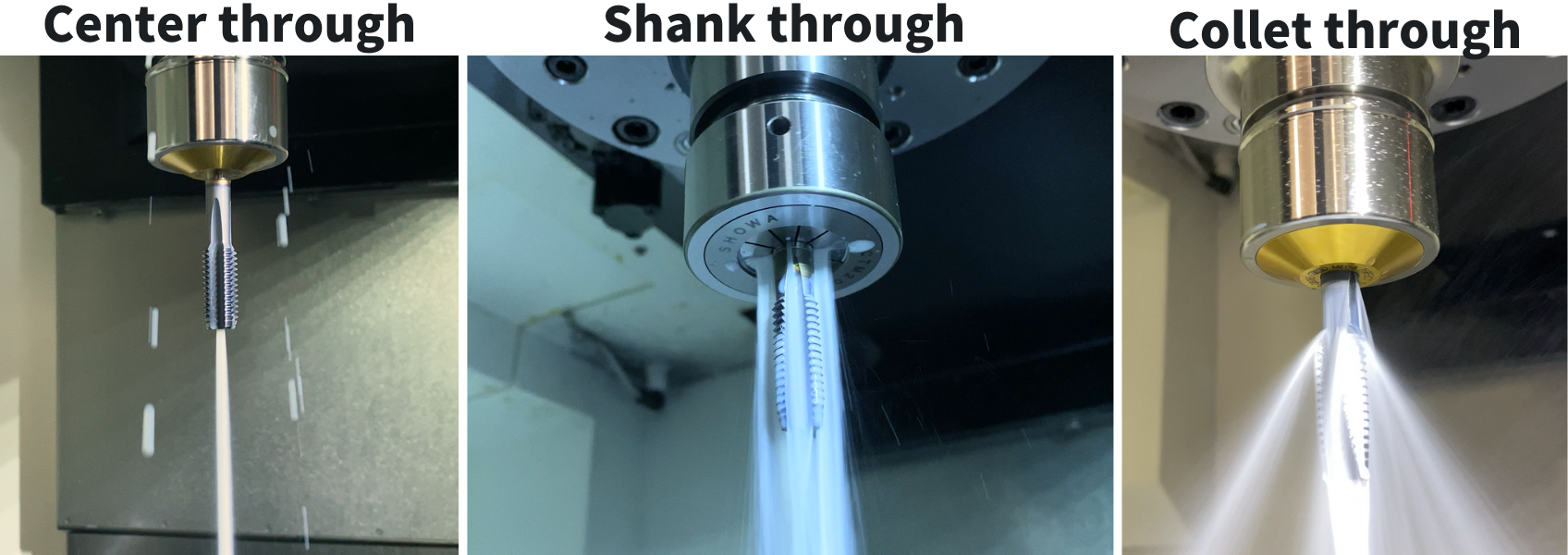
The blind hole comparison
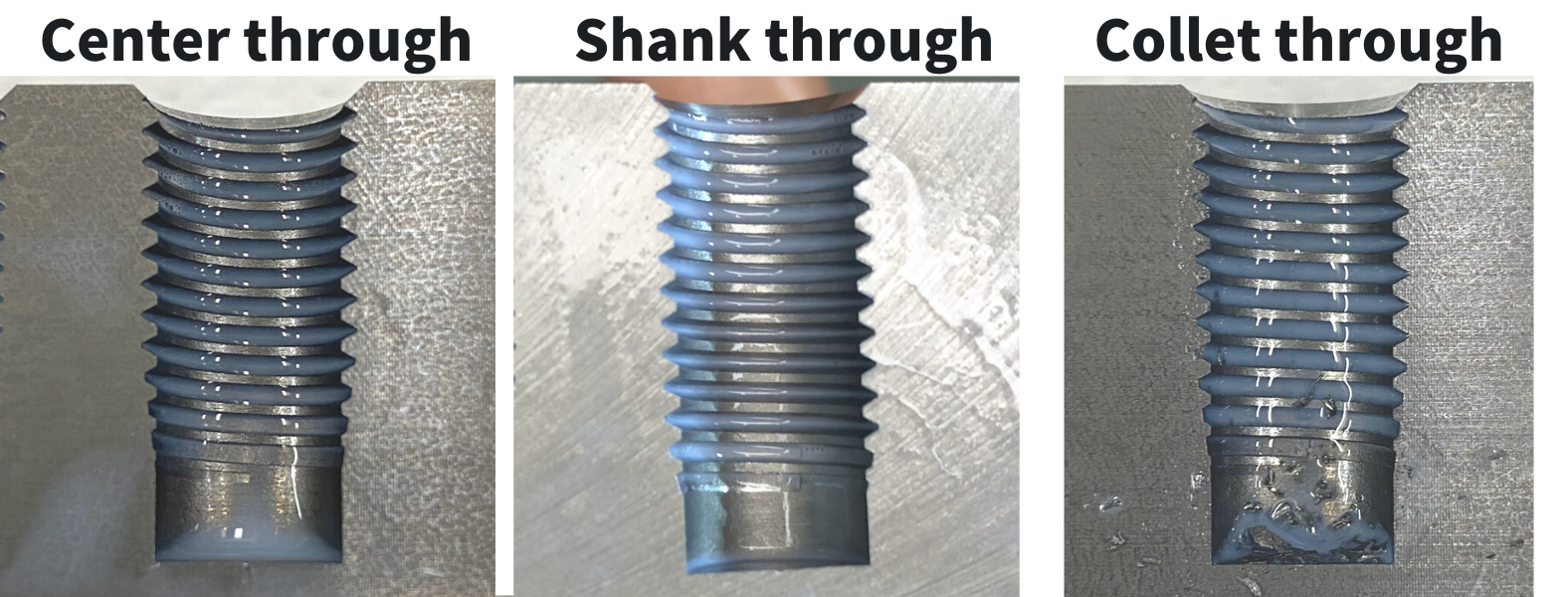
Result:
In the center through and the shank through, it was good chip evacuation at both the bottom and the threaded part.
On the other hand, in the collet through, chips do not evacuate well at the bottom of the hole, and chips remained at threaded part as well.
The through hole comparison
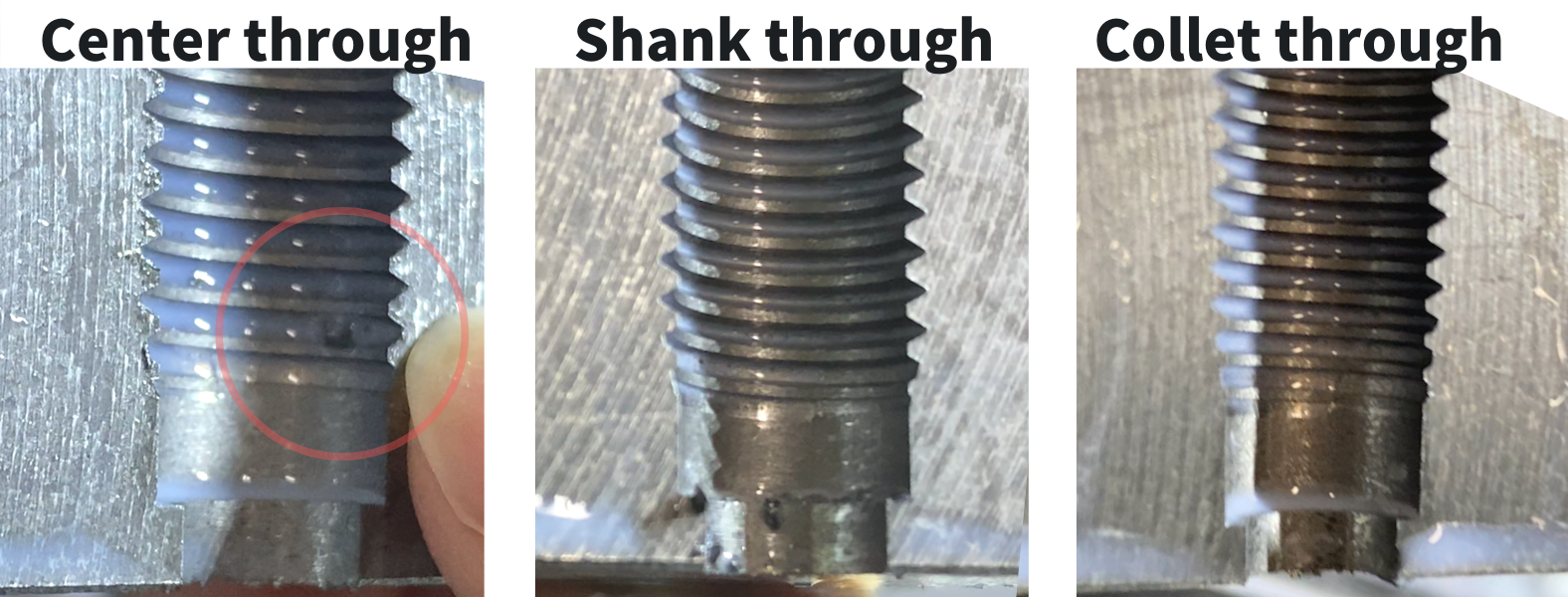
Result:
In the center through, a lot of chips remained on the threaded part which means the coolant is not properly supplying. The shank through had chips remain on the bottom, but no chips remain on the threads. Short projection tap of collet through was excellent chip evacuation, there is no chip remain on flat part and threading part.
Depending on the equipment with high coolant pressure and the projection of tap, the result of shank through and collect through may be reversed in case of the through hole.
Explanation video
Chip evacuation performance comparison of taps
Short video
Parody video ver.
The chip control performance reality show.